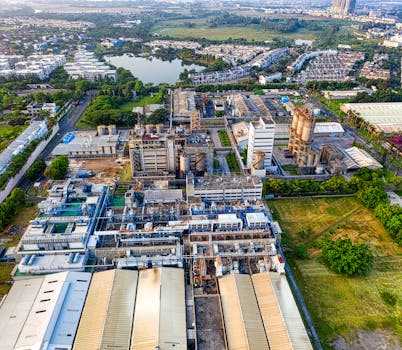
**
Gradiant's Pennsylvania Breakthrough: Revolutionizing Lithium Extraction from Oilfield Wastewater
The burgeoning need for lithium, a critical component in electric vehicle batteries and renewable energy storage, has spurred innovation in its extraction. Gradiant, a leader in water reuse and resource recovery technologies, has announced a significant leap forward with the launch of its innovative lithium production facility in Pennsylvania. This facility marks a pivotal moment in the sustainable sourcing of lithium, extracting the valuable metal from oilfield-produced water – a previously underutilized and often problematic byproduct of oil and gas operations. This groundbreaking project positions Pennsylvania at the forefront of the burgeoning lithium industry and promises significant environmental and economic benefits.
Harnessing a Waste Stream: Turning Oilfield Wastewater into a Lithium Resource
For years, oilfield-produced water (also known as O&G produced water) has posed a significant environmental challenge. This highly saline wastewater, a byproduct of oil and gas extraction, often contains dissolved minerals, heavy metals, and radioactive materials. Traditional disposal methods are costly and environmentally damaging. Gradiant's innovative approach transforms this waste stream into a valuable resource, extracting lithium and simultaneously treating the water for safe reuse or disposal. This represents a paradigm shift in how we approach both waste management and critical mineral sourcing. The Pennsylvania facility utilizes Gradiant's proprietary direct lithium extraction (DLE) technology, a process that offers several advantages over traditional methods like brine evaporation ponds.
Key Advantages of Gradiant's DLE Technology:
- Reduced Environmental Impact: Minimizes the environmental footprint associated with traditional lithium mining and brine evaporation, reducing land use and water consumption significantly.
- Faster Extraction Time: DLE offers a significantly faster extraction process compared to traditional methods, leading to quicker return on investment.
- Higher Purity Lithium: The process yields high-purity lithium, suitable for battery manufacturing and other high-demand applications.
- Cost-Effective Solution: By utilizing a readily available waste stream, Gradiant's technology presents a more cost-effective approach to lithium production compared to traditional mining.
- Sustainable Resource Management: The technology promotes circular economy principles by transforming waste into a valuable commodity.
Pennsylvania's Strategic Role in the Lithium Supply Chain
The location of Gradiant's new facility in Pennsylvania is strategically significant. The state possesses abundant oil and gas reserves, generating substantial volumes of oilfield-produced water. This readily available feedstock provides a consistent supply for the lithium extraction process. Moreover, Pennsylvania's location within the United States strengthens domestic lithium production, reducing reliance on foreign sources and enhancing energy security. The project aligns perfectly with the growing demand for domestically sourced critical minerals, a key element of national strategic goals for energy independence and economic growth.
Economic and Environmental Benefits for Pennsylvania:
- Job Creation: The facility's operation will create numerous high-skilled jobs in engineering, operations, and maintenance.
- Economic Diversification: The project diversifies Pennsylvania's economy, moving beyond traditional industries towards a more sustainable future.
- Reduced Water Pollution: The treatment of oilfield-produced water significantly reduces water pollution and protects local ecosystems.
- Improved Resource Management: The project demonstrates effective resource management, transforming waste into a valuable asset.
Direct Lithium Extraction (DLE): A Game Changer in Lithium Production
Gradiant's success hinges on its proprietary DLE technology. Unlike traditional methods that involve large-scale evaporation ponds, DLE employs advanced membrane technologies to selectively extract lithium ions from the produced water. This process consumes significantly less energy and water, resulting in a smaller environmental footprint. Furthermore, the high purity lithium produced using DLE is immediately suitable for battery manufacturing, eliminating the need for further refining steps. The technology’s adaptability is also noteworthy; it can be scaled to accommodate varying volumes of produced water, making it suitable for deployment in diverse geographical locations.
The Future of Sustainable Lithium Production
Gradiant's Pennsylvania facility represents a significant milestone in the quest for sustainable lithium sourcing. The successful deployment of its DLE technology showcases a viable pathway for extracting this critical mineral while mitigating environmental impacts. This model has the potential for replication across other oil and gas regions globally, offering a sustainable solution to both lithium demand and wastewater management. The project highlights the importance of innovation in resource management and the potential for transforming waste streams into valuable assets. As the world transitions towards a cleaner energy future, Gradiant's technological breakthrough ensures a more sustainable and secure supply of lithium, a key element in this transition. The impact extends beyond just lithium production; it signals a new era in responsible resource management and a commitment to a more sustainable future. The Pennsylvania project serves as a shining example of how technological innovation can address pressing environmental challenges while simultaneously fostering economic growth and energy independence. The project's success underscores the potential for collaborative partnerships between industry, government, and research institutions to drive transformative change in the global energy landscape.